Creating homes and structures from scratch is a rewarding career path for many. However, working in construction has unique risks and stressors. Exposure to harmful chemicals, constant loud noise, handling heavy loads, and potential hazards such as falling from a high place or electric shocks are among the daily risks for millions who work on construction sites.
Hence, construction is the sector with one of the highest rates of fatal workplace accidents, according to the International Labor Organization (ILO). The organization estimates that 2.3 million workers around the world lose their lives to work-related accidents and illnesses every year.
Even though these figures have been improving in some parts of the world with stricter regulations, construction companies must up their games to prevent these devastating consequences.
As we’re observing World Health Day on 7 April, we created a list of suggestions the executives could follow to boost occupational health in construction.
Continuous Risk Assessment and Inspection
According to the US Occupational Safety and Health Administration, construction has a “fatal four” — four common workplace accidents that cause most of the damage. These include falls, being struck by objects, electrocutions, and being caught in between equipment or objects.
The “fatal four” accidents often happen not due to subtle miscalculations, but due to significant oversights that could have been prevented with a continuous risk assessment and inspection at construction sites. Hence, site managers must have a proactive approach to identify any hazards, analyze which workers suffer from the highest risk, and implement procedures to control them.
Enforcing Protective Gear
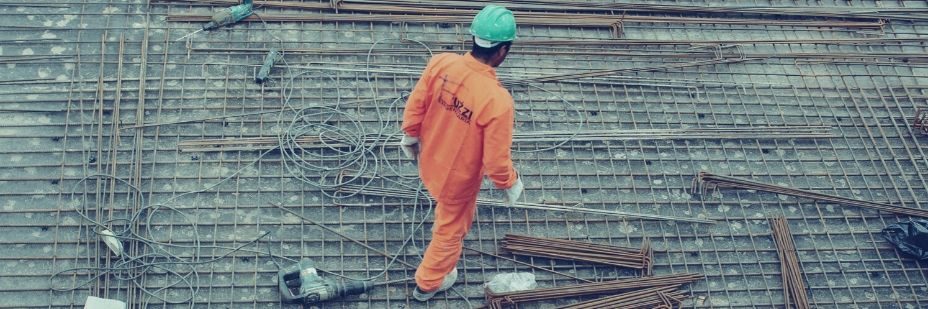
The minimal protective gear for everyone present at a construction site to wear is hard hats and safety glasses. However, the risks that every construction employee face during work differ.
Once the field managers are aware of all the threats and risks at their sites, they must assign appropriate protective equipment for each employee. Personal protective equipment (PPE) in construction broadly shields five areas. There are numerous items designed to protect the eyes and face, feet, hands, head, and hearing.
Furthermore, high-visibility clothing is another essential strategy to reduce the risks of accidents known as “run-overs” or “back-overs”.
Rigorous Training
Before any employee steps on a construction site, rigorous training in health and safety is imperative for them to understand the risks, protect themselves and their colleagues. Depending on their tasks and responsibilities at the site, they might benefit from further specialized courses like cranes and rigging, fire safety, fall protection, or industrial hygiene.
Innovative site managers might also tap into technologies like Augmented Reality and Artificial Intelligence to facilitate a faster and more efficient process of training.
Encouraging Regular Breaks
In a loud and high-stress environment that construction sites can be, even the most veteran operators might suffer from fatigue. Towards the end of a long day, their reflexes might start slowing down. Hence, site managers must ensure that all workers are taking regular breaks to rest and rejuvenate.
For on-site and stand-by shifts, the ILO recommends a minimum of 90 hours of resting time weekly, with at least one unbroken 24 hours. Furthermore, in some situations like high-stress shifts, security roles, or working away from home, construction employees might be entitled to a compensatory rest.
Managing Stress at Work
Research shows that construction is among the most stressful sectors. 82 percent of the workers feel stressed at least some part of their weeks. Stress can trigger a myriad of physical and mental health problems while increasing the risk of errors.
In the meantime, some studies confirm that speaking about stress and sharing common feelings alone can reduce stress. Hence, to create a safer working environment and boost employee well-being, construction managers must encourage a healthy dialogue on their sites.
Educating employees about stress management and giving them mental health first aid training can galvanize these efforts for further improvement.
Digital Modelling to Optimize Occupational Health
Many executives in the construction sector are no strangers to the benefits of Building Information Modeling (BIM): It saves costs, time, cuts waste, and helps teams to push creative boundaries.
In addition to these benefits, BIM also boosts safety. This planning tool allows the architects and builders to gain a bird’s eye view of their construction projects. Hence, planning teams can take all the necessary measures to prevent accidents before they happen.
Furthermore, it’s not uncommon for construction companies to have a disconnect between their headquarters and fieldwork. Cases as such might alienate some employees and compromise their well-being. The right communication and seamless collaboration among teams are vital to avoiding these problems.
By tapping into technologies such as Building Information Modeling (BIM), site managers can boost occupational health in construction and create more inclusive, efficient, and safer environments.